Evaluating Technologies for Extruding Barrier Films
A closer look at crystallinity within coextruded films
Coextruded films play a vital role in packaging thanks to their inherent cost-effective versatility; they can be manipulated to provide a wide range of functionality such as strength, barrier, optics and shrink, and provide light-weight packaging solutions. As flexible polymer packaging continues to gain market share from paper, metal and glass types, the need for new plastics structures and added production continues to grow.
Along with this growth come new challenges as packaging industry standards are becoming increasingly more demanding. The requirement to protect the product from microbial degradation, physical damage, and chemical changes, combined with the need to offer attractive shelf appeal presents a challenging combination. Film producers must have a solid foundation of how films are made and what processes influence the final properties of films in order to fully reap the benefits of coextrusion technology. After all, multilayer film structures allow flexibility to create and fine-tune packaging film designs; exploring the technical and economical limitations of new film structures can lead to profitable innovations.
The manner in which multilayer films are coextruded, be it by blown, cast or biaxially-oriented by annular die (commonly referred to as bi-oriented, or biax) extrusion methods, impact the mechanical, thermal, barrier and optical properties of the films they produce. The focus of this article is crystallinity within the film, how it is formed and the influence that crystallinity has on the final film.
When polymer melt exits the extrusion die head, whether it be a flat die utilized by the cast process or an annual die used in blown or bi-oriented processes, it is cooled to produce a structure comprised of both crystalline and amorphous phases. Since these polymer products consist of both crystalline and amorphous phases, they are often referred as ‘semi-crystalline’ materials. The ratio of each phase can be very different depending on polymer characteristics, the method of extrusion and processing parameters, such as extrusion temperatures and film forming/cooling rates. The crystalline phase can also consist of a range of crystal sizes and crystal density, all of which are used to characterize the “crystalline morphology” of the film, which can impact a range of film properties.
For semi-crystalline polymers, there are three important temperature characteristics: Melting Temperature (Tm), Crystallization Temperature (Tc) and Glass Transition Temperature (Tg).
They are often represented as Tg < Tc < Tm.
If the semi-crystalline polymer has a Tg that is below ambient temperature, the amorphous phase will be rubbery and the polymer is classified as semi-crystalline rubbery polymer.
Example semi-crystalline rubbery polymers - Tg of polymer below ambient temperature (25°C):
LDPE: Tg ~–50°C; Tc ~95 °C; Tm ~114°C
LLDPE: Tg ~-95°C; Tc~ 110°C; Tm ~ 124°C
If the polymer has a Tg that is above ambient temperature, the amorphous phase will be glassy and the polymer is classified as semi-crystalline glassy polymer.
Example semi-crystalline glassy polymers - Tg of polymer above ambient temperature (25°C):
Nylon 6: Tg ~55°C; Tc ~130-160 °C; Tm ~220°C.
EVOH: Tg ~50°C; Tc ~140-160 °C; Tm ~160°C.
Taking a closer look at the two phases that comprise the semi-crystalline film structure, the amorphous phase and the crystalline phase, reveals how their presence affects film properties.
Amorphous Phase
The amorphous phase is comprised of randomly oriented polymer chains in the cooled film. The nature of this phase is closely linked to the polymer’s Glass Transition Temperature (Tg). When the ambient temperature is below the polymer’s Tg, the polymer in the amorphous phase behaves like a glassy material and has a very low chain mobility. When the ambient temperature is above the polymer’s Tg, the polymer behaves like a rubbery material and polymer chains have excellent mobility.
Films that consist primarily of amorphous phase tend to be very transparent due to the limited number of crystals present to scatter light. The polymer chains are frozen in random configuration and thus have less intermolecular interactions, making the film weaker in terms of lower tensile strength and modulus. Also due to the random orientation, these films have excellent elongation properties and, depending on orientation, resist tearing. Since the polymer chains in amorphous structures are held together with weak forces, the resulting films have restricted dart and puncture resistance. Films with higher amorphous content also have lower heat resistance.
Crystalline Phase
Polymer chains within a crystalline phase are packed in ordered configurations typically referred to as a crystal lattice. The nature of this phase is linked to the polymer’s Crystallization Temperature (Tc). If the polymer melt is cooled slowly when creating a film, crystals will form at Tc. If this plastic film is reheated, the crystals will melt at the crystalline Melting Temperature (Tm) of the polymer.
It is very important to note that two different films may have equaly percentage of crystallinity, but one film may have a low number of large size crystals while the other film may have a large number of small size crystals. This distinction can create significant differences between the properties of the film.
Films with high crystalline content tend to be hazy, especially in films with large crystals, which scatter light more effectively than smaller ones. In the case where the crystalline structure dominates with a large number of very small crystals, the film’s gloss may also be improved as a result of the surface morphology. Due to the close vicinity of polymer chains in the crystal lattice, there are increased intermolecular forces (dipole –dipole type for PE film or hydrogen bonding in polar polymers like PA/EVOH) giving the film high tensile strength and modulus. When the crystalline phase is characterized by a large number of small crystals, additional intermolecular forces will exist to make the film even stronger. These small crystals are less fragile than large crystals and result in a film with improved dart and puncture resistance properties. However, this configuration of a high density of small crystals produces films that have low machine-direction/transverse-direction (MD/TD) tear strength because of the increased amount of interfaces that exist between the amorphous and crystalline phases, which serve as weak areas for tear propagation.
The amorphous content of any semi-crystalline film allows for elongation, so the less amorphous content the film has, the less extensible it will be. Moreover, films with crystalline structures comprised of a large number of small crystals will be even less extensible.
Crystalline content provides a higher barrier than the amorphous content of the film because the polymers chains are tightly packed in crystal lattice where permeates, such as oxygen and moisture, have lower diffusion. Besides this, permeability of permeates can also differ greatly through crystalline and amorphous phases.
Extrusion Methods
Different methods of cooling polymer melt produce different effects on crystallinity in the final film produced. The type of cooling used (air vs. water vs. cooling roll), and the additives and resins that are processed can affect the size and density of crystals formed in the film. Certain extrusion methods, such as cast vs. blown, tend to lend themselves to certain crystalline configurations as a result of the varying rates of melt cooling.
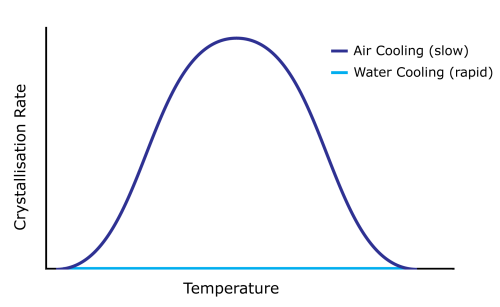
When a polymer melt is cooled slowly, the randomly oriented polymer chains in the melt will start to reconfigure into an ordered configuration - a crystal lattice. Some portion of the polymer chains in the melt will be ‘frozen’ while still in a random configuration to produce the amorphous component of the film structure.
When a polymer melt is cooled rapidly, the randomly oriented chains in the melt freeze quickly to produce a film structure that is predominantly amorphous; yet, some crystalline component will also be obtained.
Blown Film Coextrusion
With conventional blown film processes the polymer melt is cooled using air from a cooling ring and/or an internal bubble cooling (IBC) system. This process of air-cooling is relatively slow in ‘freezing’ the film structure and generates a significant proportion of crystalline content in the final film.
Moreover, blown film crystalline morphologies are generally composed of a crystalline phase with large crystals. As a result of this crystalline morphology, blown films tend to have high tensile strength and modulus, improved barrier properties, and fair elongation. Blown films, depending on materials used, will have good heat resistance, making them suitable for hot-fill applications. Due to the crystallinity in blown films they are likely to be more hazy than a similar film produced by the cast method.
Having uniform air flow and air temperature in the air ring and IBC is important to develop consistent crystalline morphology. If film fabrication is done in summer or winter, day or night, dry or humid environments (i.e. without conditioned production hall), the film’s crystalline morphology can be altered to some extent and can influence the film properties.
It is also of important to have uniform individual layer gauge and overall gauge, in which the extrusion die head plays a critical role, because thin and thick spots cool at different rates and will create changes to the crystalline morphology that will impact film properties.
Cast Film Coextrusion
During cast coextrusion, the polymer melt is cooled rapidly through contact with efficient heat transferring cast rolls to quickly ‘freeze’ the melt. This rapid quenching of the melt produces films with a large amorphous component and a very small amount of crystalline phase. Since cast coextrusion process produces films that are dominated by the amorphous phase, cast films are weaker (lower tensile strength and modulus), have low heat resistance and have inferior barrier properties to blown or bi-oriented films (with respect to crystallinity influences). They exhibit excellent elongation and excellent transparency, making them highly suitable for thermoforming applications.
Bi-oriented Film Coextrusion
The annular bi-oriented film coextrusion process consists of an initial quenching of the tube of film extruded from the die head, followed by the formation of a second and sometimes third bubble to create the desired film properties. These secondary and tertiary processes include orientation and annealing, which can be manipulated to control the orientation and shrink characteristics of the final film.
In the bi-oriented process the primary tube (first bubble) is cooled very rapidly by water to create a film structure that is dominated by the amorphous phase. The small crystalline phase is composed of very small crystals. The primary tube is then reheated above Tg but below Tc and drawn into a second bubble. The small crystals formed in the initial quenching process can act as nucleating sites to produce a final film with a large number of very small crystals. This results in films that are very strong, with improved dart and puncture resistance, enhanced barrier properties, good transparency and excellent gloss. Bi-oriented films, by comparison to blown and cast films, offer poor elongation and weak MD/TD tear resistance properties.
Conclusion
It is important to note that different extrusion technologies generate varying crystalline morphologies in the final films they produce as a result of the varying melt cooling techniques and, in the case of bi-oriented films, the reheating process. These varying crystalline morphologies affect the functional properties of the films, such as the film’s strength, barrier properties, elongation and appearance. Understanding these differences and predicting how these changes will occur can create innovations in film structure designs that may open the door to new opportunities.
Disclaimer: The information provided is based on general trends observed by each process. Specific materials will yield differing results and expected properties should be predicted on a case-by-case basis as they relate to processing parameters, coextrudate materials and film configurations.