Understanding Screw Design for Film Extrusion Process
Hassan Eslami, PhD
Rheologist, Macro Engineering and Technology
The screw is the heart of the extruder and a key component of any film extrusion system. The screw melts the polymer, prepares the homogeneous melt and pumps the melt through the die. Special attention needs to be taken into account while designing screws for the film extrusion process, particularly for multilayer barrier film extrusion, due to both the complexity of the process and the complex rheology of the materials being processed. The extruder is a key component of any extrusion process.
The plasticating screw, commonly referred to as the heart of the extruder, is the most important part of the extruder; making its design critical to the success of any film extrusion system. A properly designed screw for film extrusion processes should completely melt the pellets, homogenize the melt and develop an appropriate melt temperature and pressure before delivering the melt to the die. The mechanical and optical properties of the final film highly depend on the quality of the melt being delivered to the die. Designing a screw for film extrusion process is often challenging due to the complexity of the process. For example, gauge uniformity of the final film is very sensitive to the thermal homogeneity of the polymer melt. When it comes to multilayer barrier films, the screw design becomes even more challenging due to the complex rheology of the barrier materials such as Polyamide and PVdC. Each screw used for multilayer barrier film extrusion must be designed based on the corresponding rheology in order to achieve the desired structure with uniform film thickness and without compromising other required properties, such as mechanical and barrier properties. This article begins with an explanation of basic screw geometry. The effects of the compression ratio, L/D ratio, flight clearance, barrier and mixing sections on screw performance are then discussed. Finally, the relationship between the rheological properties of the materials being processed and the screw geometry will be explored

Figure 1: Schematic representation of a simple metering screw.
Screw geometry
Figure 1 provides a schematic representation of a simple metering screw. It is composed of three main sections; the feed section, transition section and metering section. The feed section, which is often also referred to as the conveying zone, is responsible for conveying materials (pellets, fluff and powder) forward to the transition section. The transition section is the portion of the screw where the majority of the melting takes place. The metering section, also called melt conveying or pumping zone, delivers the melt toward the discharge end of the extruder.
Screw channel depth, one of the most important variables in screw design, usually has its largest value in the feed section and smallest value in the metering section. The channel depth gradually decreases along the transition (or compression) section which allows more work to be applied to the polymer. The feed and metering sections have constant root diameters along their lengths, making the channel depths constant in these zones.
The bulk properties and the frictional properties (i.e. pellet-barrel, pellet-screw and pellet-pellet coefficients of friction) of the materials being processed are the most important parameters used to design the screw geometry in the feed section. The rheological as well as the thermal characteristics of the materials being processed become important in specifying screw geometry in transition and metering sections.
Compression Ratio
Compression ratio is an important parameter to asses during screw design. It can be defined by the ratio of the channel depth (or alternatively channel volume) in the feed section to that in the metering section. The former is known as depth compression ratio and the latter is called volumetric compression ratio. Compression ratio (CR) is usually used instead of depth compression ratio and it is defined as indicated.

For special screws, like barrier screws, considering the volumetric compression ratio (VCR) is a more reliable design parameter than depth compression ratio (CR) as flight pitch is also changed from the feed section to the transition and metering sections in the design of these screws.
It is worth mentioning that the value of the CR can also be a misleading parameter in screw design. For example, if the channel depth changes from 16 mm in the feed section to 4 mm in the metering section, the CR is 4:1. However, the same compression ratio will be achieved if the channel depth changes from 12 mm in the feed section to 3 mm the metering section. These two screws behave completely different despite the fact that they have an identical compression ratio. An important parameter in screw design, which is closely related to the compression ratio, is the slope of the transition section. In order to achieve efficient melting, the compression ratio and the slope of the transition section should be carefully matched with the melting rate of the polymer being processed. Screw compression ratio also depends on the compressibility of the materials being processed. Compressibility, the ability of loose materials (e.g. fluff) to occupy less volume while compressed, affects the melting efficiency of the materials being processed. Therefore, using a screw with a high compression ratio is generally recommended for processing materials with high compressibility.
Length-over-diameter (L/D) ratio
Another key parameter in screw design is the length-over-diameter (L/D) ratio. It is defined as:

Typical screw L/D ratios lay between 20: 1 to 34: 1. The length of the screw depends on the number of sections being considered in screw design, which in turn, depends on the application and the materials being processed. For conventional screws with three functional zones (i.e. feeding, compression and metering zones), the typical L/D ratio is 24:1. However, for film blowing and film casting processes where highly homogenized and gel-free melt with constant temperature and pressure are required, the need for additional sections is inevitable. For example, one or more additional mixing elements are often added to the design of these screws to ensure an even melt is delivered to the die. Therefore, for these applications the screw should be longer to accommodate the added sections. The typical L/D ratio for screws used for film extrusion processes is 30:1. For processes where degassing is required (the so-called two stage screw), usually screws with L/D ratio of greater than 32:1 are recommended.
Flight Clearance
Flight clearance is a measure of the space between the screw’s outer diameter and the barrel wall. As a rule of thumb, it is considered to be 0.1% of the screw diameter. Inappropriate flight clearance will have an adverse effect on screw performance; small clearance can cause excessive wear on the screw flights, while large clearance can diminish the melting efficiency of the screw. The latter occurs because large flight clearances can allow for a thick melt film to be accumulated on the surface of the barrel, which reduces the thermal conductivity through the barrel. Large flight clearance may also reduce the pumping capability of the screw because of the excessive leakage flow (melt flowing over the screw flight). Barrier screw versus standard metering screw A potential problem for standard metering screws is inefficient melting, particularly at high screw speeds. Efficient melting may occur in a standard metering screw if the solids bed remains packed throughout the transition section. However, this is not always the case as the solids bed often breaks up at high screw speed (see Figure 3).
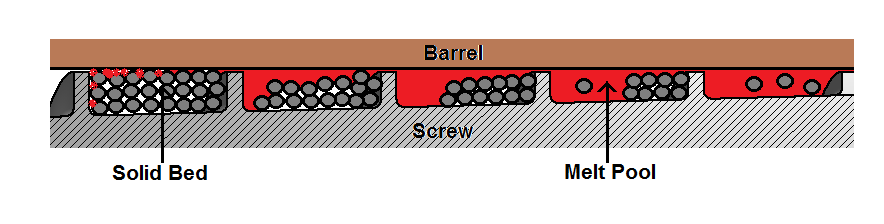
Figure 3: Progress of melting in a standard metering screw, solids bed break up occurs at the end of the transition section.
Once the solids bed breaks up, the remaining unmelted pellets can only be melted through heat convection from the surrounding melt. Melting through convection is not an efficient melting mechanism for polymeric materials due to their limited thermal conductivity. Therefore, unmelted polymer may still flow through the discharge end of the extruder, resulting in undesirable product. Barrier screws can overcome this problem by separating the melt and solid channels using a secondary flight called a barrier flight. The barrier section, where the main portion of the melting occurs, is placed between the feed and metering sections. The barrier section is typically a replacement of the transition section; however, there are screw designs with separate transition and barrier sections. There are many different designs for barrier screws yet they all follow the same principle of keeping the solids bed and melt pool separated, as shown in Figure 4. A properly designed barrier screw results in higher output rates and lower melt temperatures due to their higher melting capability.
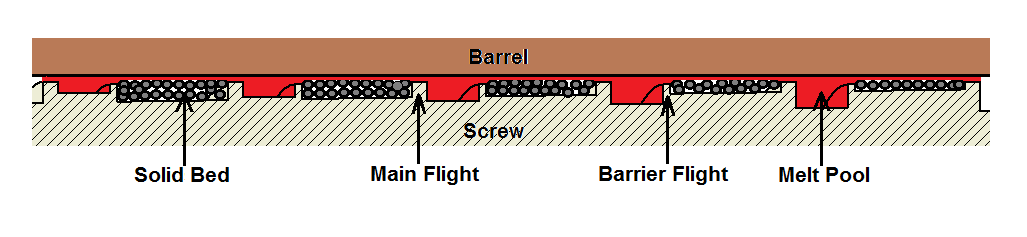
Figure 4: Progress of melting in a barrier screw
As illustrated in Figure 5, there are two main designs for barrier screws; constant depth and constant width. As the name suggests, the depth of the melt and solid channels remains unchanged with the constant depth design. The width of solid channel becomes narrower along the length of the screw while the melt channel becomes wider. In contrast, constant width barrier screws have melt and solid channel widths that remain unchanged throughout the barrier section while their depths vary; the solid channel depth decreases and the melt channel depth increases.
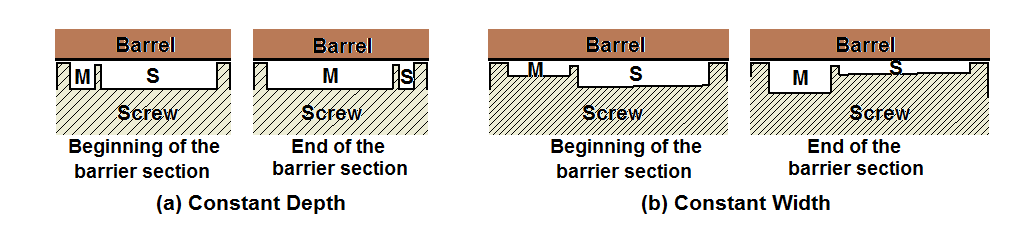
Figure 5: Two types of barrier design, M: Melt channel, S: Solid Channel
Mixing Section
Nowadays, almost all screws used for film extrusion processes have some sort of mixing element. This is because obtaining good film quality requires very high quality melt to be delivered to the die, which is not easy to achieve without a mixing section in the screw. In principle, two types of mixing occur in the extruder; dispersive mixing and distributive mixing. For film extrusion processes, dispersive mixers are mainly used to remove gels in the melt. Distributive mixers are used for melt homogenization, particularly for obtaining thermally homogenized melt. This is an important issue in film extrusion processes since poor homogenization has a detrimental effect on the final film quality, particularly on its gauge uniformity. Melt temperature also has an important effect on the optical properties of the final film. Many types of mixing elements have already been developed for both dispersive and distributive mixing. The most widely used mixing elements for film extrusion processes are Maddock type mixers and Pineapple mixers. The Maddock (or Union Carbide) mixer, known as a high shear mixing element, contributes not only to dispersive mixing but to distributive mixing as well. This mixer is also known for its high melting capability. In principle, high shear mixing elements are mainly used for dispersive mixing; however, in the screws designed for film extrusion processes, Maddock mixers usually play the role of a complementary melting section, which helps avoid the presence of unmelted polymer at discharge end of the extruder. It should be noted that high shear rate and consequently high shear stress applied to the polymer melt while traveling over the small gap of the barrier flight may raise the polymer melt temperature. Twisted Maddock mixer, also called spiral shearing mixer, with an optimized shearing and wiping flight width can reduce the effect of shear on melt temperature rise. The Pineapple mixer, normally used as distributive mixer, continuously splits and recombines different streams of the melt to obtain homogenous polymer melt. It is known as a low shear mixing element. For film extrusion processes where thermally homogenized melt is a must this mixer can be very helpful. Other kinds of distributive mixers, such as pin-type mixers, can also be beneficial for thermally-sensitive materials like PVC for their ability to distribute the melt without applying high amount of shear.
Rheology
It is well established that the rheological properties of the polymer play an important role in the design of the screw and its performance. Rheologically speaking, there are two different types of flow taking place at the extruder screw; shear flow and shear-free or elongational flow. Even though there are some sections in the screw where the elongational flow plays a role (e.g. some parts of mixers), the flow in the screw channel is mainly dominated by shear. Therefore, the shear flow characteristic of the molten polymer being extruded is a critical parameter to examine when determining the appropriate screw design. Figure 6 is a representative plot of shear viscosity versus shear rate, which illustrates the typical flow curve for polymeric materials. The flow curve consists of three regions. Region I is the portion of the curve where the shear rate is low. This region is often referred to as the Newtonian Region as the viscosity has a constant value, called zero-shear rate viscosity. Region II is a transition region where the viscosity changes nonlinearly with shear rate. Finally, Region III is a shear-thinning region in which the viscosity decreases with shear rate. The slope of the shear viscosity versus shear rate in this region, when plotted on double logarithmic scale, is used to determine the power-law index. The power-law model is frequently used to express the relationship between shear viscosity and shear rate in the shear-thinning region. Power-law index is a measure of the shear sensitivity of the polymer. A smaller value of the power-law index indicates that the behavior of the polymer is more shear-thinning.
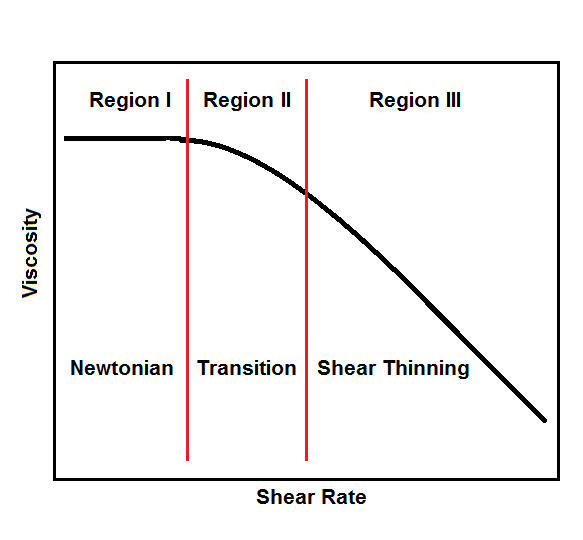
Figure 6: Typical flow curve for polymer melts
Specifying the screw’s geometrical dimensions (channel depth, helix angle, pitch and flight clearance) and designing the barrier and mixing sections must be done with careful consideration to the viscosity curve of the material being processed. For example, for low viscosity materials, the screw channel in metering section should be relatively shallow while for high viscous materials it should be relatively deep. It is worth mentioning that melt index (MI) which is an engineering measure of the melt viscosity corresponds to the value of the shear viscosity at one specific point. Using melt index instead of flow curve in screw design will lead to improper screw geometry. The screw helix angle is usually designed to be 17.66. This helix angle corresponds to the square pitch. However, this is not always the optimal screw helix angle. In fact, there is a relation between the screw helix angle and the power-law index of the viscosity curve. More specifically, with increasing the power-law index, the optimum helix angle increases. In other words, shear sensitive materials require smaller screw helix angles while less shear sensitive materials need larger screw helix angles. For sensitive materials, like PVdC and Polyamide, determining the optimum value of the helix angle is critical to successful extrusion. The key challenge in designing a screw for processing thermally-sensitive barrier materials like PVdC and Polyamide is that the screw design should permit as short a residence time in the extruder as possible while conveying a highly homogenized melt to the die entrance. In other words, the screw design must permit the fundamental objective of the extruder to occur successfully in less time; otherwise, the polymer may degrade. At the optimum processing condition, short residence time requires shorter screw length which means a smaller screw L/D ratio is necessary. With a shorter screw, less room is available for the mixing elements that homogenize the melt. Therefore, the lengths of each functional section of the screw have to be carefully calculated based on the rheological and thermal properties of these polymers.
The properties of the final film obtained from film extrusion processes are directly related to the quality of the melt at discharge end of the extruder. Successful screw design will deliver homogeneous melt with constant temperature and pressure to the entrance of the die. For appropriate solids conveying, the pellets should have a high degree of stickiness on the barrel and high degree of slippage on the screw surface. For efficient melting, the screw geometry should be carefully matched with the melting rate of the polymer being processed. An appropriate barrier screw design results in higher output rate and lower melt temperature due to their higher melting capability. Mixing section is necessary for screws used in film extrusion processes as these processes require highly homogenized melt. The rheological properties, particularly the curve of the shear viscosity versus shear rate, should be taken into account while designing any plasticating screw.