Prestretched Film Production
in a Single Shot
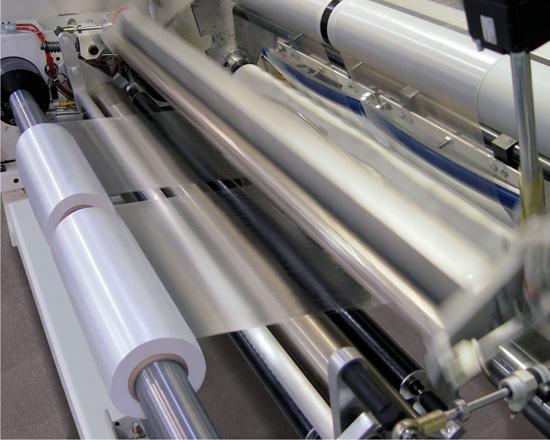
Stretch films have been used for decades as an efficient and inexpensive way to secure items for transport. Applied by machine, or by hand, these films are unwound from rolls, stretched and then wrapped around items to be secured. By stretching the film before wrapping the load, energy is stored in the molecular bonds of the film. This energy tries to shrink the film back to its original form causing the film to cling tightly to the load and secure it in place. The film also clings to itself to provide additional gripping strength and ease in application.
Stretch films are produced on both cast extrusion systems and blown extrusion systems. Typically, cast processes produce stretch films that are both clear and glossy, and have double or triple the production capacity of blown lines, which can make justifying the return on investment easier. The key advantage for producing stretch films with the blown process is the mechanical properties they exhibit. They have much-improved puncture and tear resistance; qualities that are ideal for stretch film applications where films are stretched significantly in the machine direction.
Aside from the benefits of increased product performance, there is also a significant cost saving to having good gauge. Amidst rising polymer costs and highly competitive markets a processors ability to produce film with uniform thickness has become a necessity. It's no secret that processors spend more than 50% of their operating costs strictly on resin, masterbatches and special additives, and excessive use of these materials, particularly costly barrier and tie resins or additives, reduces the profitability of the business.
Prestretched Film Rolls
Prestretched films have evolved from traditional stretch films as they provide several benefits that give them an advantage over standard stretch films. Prestretched film, as the name suggests, is film that is pre-stretched prior to it being wound into rolls for final use. This means the film doesn't require as much stretching energy as a standard stretch film to achieve the same wrapping force; a key reason why prestretched films are popular for hand wrap.
The rolls are generally light and easy to handle, reducing operator fatigue. Operators also benefit by being able to use a walk-forward wrapping technique, which can help prevent slip and fall incidents. In terms of material costs, prestretched films are much thinner than traditional stretch films. This provides savings in resin costs and produces less waste as the operator uses less material during application. Macro's goal to enter the prestretch film market was to develop a blown film system to produce superior quality prestretch film rolls in a single process. To meet the goal the film had to be stronger and thinner but with strong edges that prevent tearing. The line was to take no trims to save on material and reprocessing costs. The rolls were to be wound with little tension to create light, soft rolls that are easier to handle and less likely to be damaged. The line was to be a single inline extrusion, stretching, slitting and winding system, all automatic. This was achieved with Macro's Blown Prestretch (BPS) Film Line.
The BPS Advantage
Macro's BPS Line creates soft, lightweight prestretched rolls that are easy to unwind and suitable for machine and hand wrapping applications. The patented process is based on an uncomplicated single-layer blown film method using an inexpensive, butene-based LLDPE with an appropriate amount of PIB or tackifier. The film is immediately tacky without the need for additional conditioning or special storage.
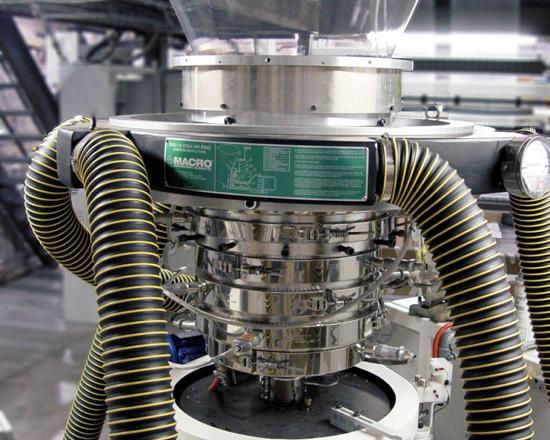
The Extrusion Process
The extruded bubble is collapsed at a low height and blocked to create a 2-ply film. This 2-ply structure provides an extra layer of strength; if there is a defect in one ply the other will cover the load. Also, line start-ups are simplified, and less time consuming as the need for individual layer separation is eliminated.
The film is then slit either 2-up or 4-up and sent to an inline stretching unit where it's thinned to 6 or 7 microns of total thickness. To retain tear strength, the stretching unit leaves the edges of the film 40-80% thicker than the rest of the film.
No trims are taken, and no scrap is created in the process. The combination of very thin film, created with inexpensive resins, and no trim or scrap generates significant savings to the processor. Not only does the processor use less resin, which is also less expensive, there is also no need for costly reclaim and conveying systems to collect trims.
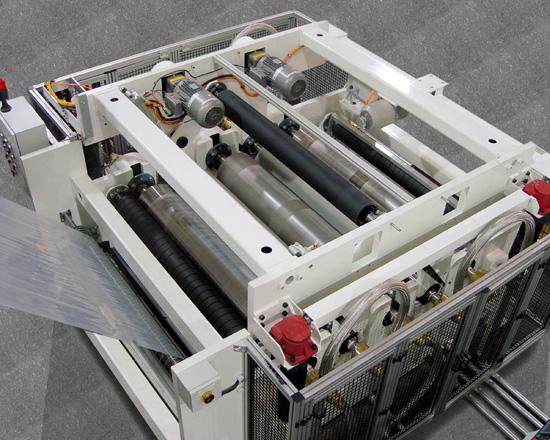
Soft Ready to Use Rolls
The film is wound on a fully automatic turret winder that is specially designed for winding soft rolls at a production speed of 500 m/min. These soft rolls are created by reducing the winding tension and deliberately entrapping air between the winding layers.
Soft rolls provide several advantages over conventional stretch film rolls:
- The rolls require less energy to unwind; making hand application easier and reducing operator fatigue.
- The rolls are more resilient than hard rolls; the edges will not damage if the roll is dropped.
- The rolls are lightweight, making them easier to handle and also less likely to cause injury if dropped on the operator's foot or hand.
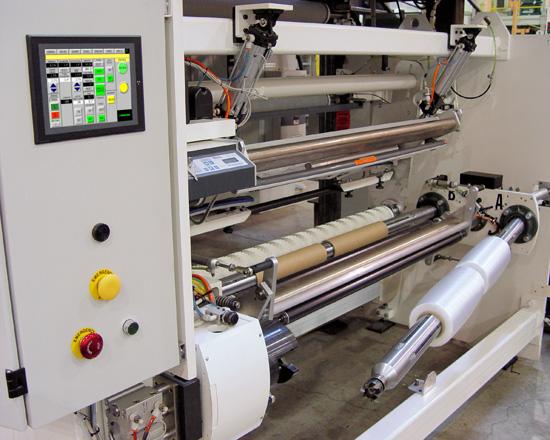
The process can be adjusted for multilayer film production using inexpensive butene copolymers in the center layer and metallocene or plastomers in the outside layers.
Macro has been awarded two US patents and one Canadian patent for this technology.
Learn more about Macro's BPS line